Consider using a hot runner mold to improve your plastic injection molding process. These molds have several benefits over cold runner molds that can lead to significant productivity improvements, better quality parts, and reduced environmental impact. Firstly, hot runner molds can reduce cycle time by eliminating the need to cool and reheat the material in the sprue and runners. This can be especially helpful for high-volume production runs. Additionally, with no sprue or runners to discard, hot runner molds can help save money on material costs and reduce environmental waste. Another benefit of hot runner molds is the ability to produce parts with better quality and consistency. Hot runner molds can reduce defects such as warpage, sink marks, and voids by keeping the material at a uniform temperature throughout the molding process. Moreover, hot runner molds offer increased flexibility in molding a wider variety of materials than cold runner molds. The heated material can be more easily controlled and flowed into the mold.
These advantages make them more reliable and safe for your plastic injection molding process. In summary, hot runner molds offer a range of benefits that can improve your injection molding process, including reduced cycle times, less material waste, improved part quality, increased flexibility, and safer operation. We could bring custom-made, flexible, and user-friendly hot runner control devices by Fiege that are one step ahead of the competition.
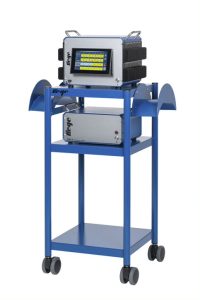
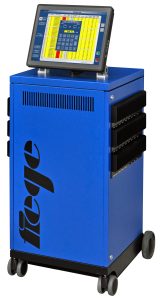
